Krzyszto Wroblew explores the growing interest in sourcing sustainable feedstocks in the tyre industry
Technologies developed over the last few years allow tyre manufacturers to design tyres with circular and sustainable raw materials. However, there’s a significant obstacle at play: scalability.
The pyrolysis industry, whose current supply capacities are insufficient, is expanding rapidly to meet demand. Tyre manufacturers would like to source recovered Carbon Black (rCB), recovered steel, and recovered pyrolysis oil as a circular feedstock to produce more sustainable carbon black grades. A solid record of quality products and growing volume would also help to drive the increasing demand for these sustainable feedstocks.
But many tyre manufacturers are still quite cautious in incorporating circularity into their business models. This is understandable as global companies need reliable partners and the rCB industry is still in its infancy. So what does the rCB industry need to do to attract more customers and succeed in increasing circularity in the tyre industries? The key is tighter collaboration to speed up innovation adoption within the industry.
Collaboration: speeding up the pace of innovation
If the tyre and automotive industries are to realise more circularity and sustainability, stronger collaboration is a crucial step in addressing some critical challenges facing the nascent rCB industry. As the rCB industry is still under development, it needs new standards to define rCB types and their quality to make the product easier to use and trust. Pyrolysis methods differ and use distinct end-of-life tyre (ELT) feedstock ratios, producing rCBs of varying composition and quality. The more standards in the industry, the more players can implement sustainable feedstocks into their manufacturing process.
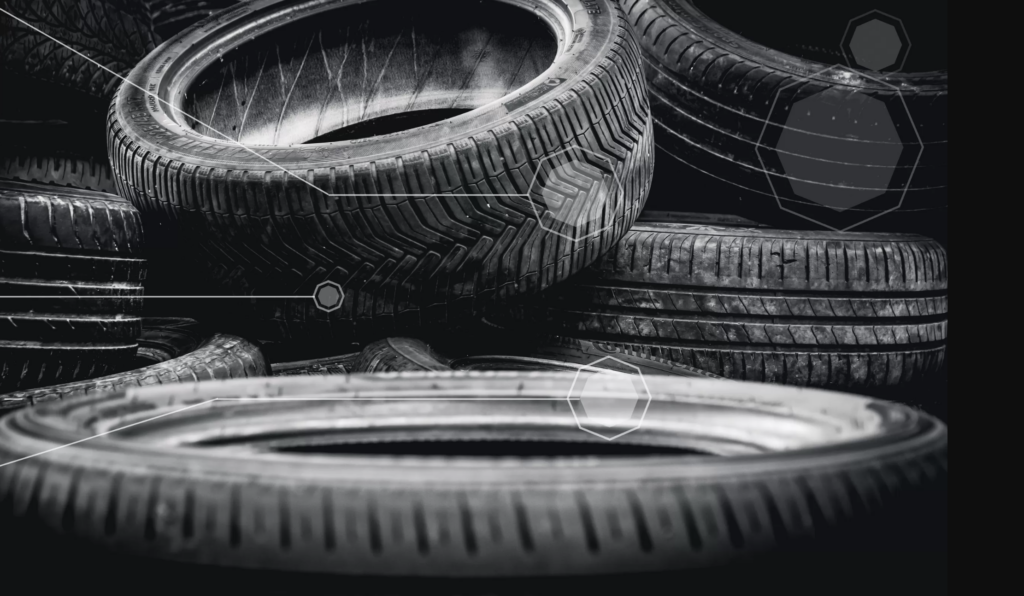
A few auxiliary technologies will also improve the pace of sustainable feedstock adoption. Companies must prepare ready-to-use rCB for specific industry needs, and collaboration is key to adjusting different parts of the rCB back end. That includes milling the rCB to a powder or pelletising and drying it to industry-required standards, ensuring the product can be handled properly by different industries and with different usage.
Then there is the need to publish more quality standards. ASTM Committee D36 is developing methods to measure rCB parameters which will allow differentiating between various rCB products and their production processes and will recommend quality control tools for producers and consumers. This will increase market adoption since quality testing will be widely available for players looking to replace virgin feedstock with a new, sustainable alternative.
Recycling solutions: a partnership example
Tyre manufacturers, rCB producers, and waste collectors can also collaborate to ensure narrow feedstock selection, which can impact the reinforcing properties of rCB, making it more attractive for specific uses. For instance, Contec collaborates with Tyre Recycling Solutions (TRS), global solutions providers for end-of-life tyre collection, processing, and recycling. Since the two share the same vision of implementing circularity within the rubber and tyre manufacturing industry, they work together to research and develop better ways of bringing recycled rubber feedstock into the tyre and automotive industry. Joining R&D and engineering efforts facilitates collaboration and innovative solutions for waste management and feedstock quality checks. One of these solutions is using specific parts of tyres as a feedstock for the pyrolysis to assess the influence on the rCB performance.
Every case study of successful, workable solutions lowers investment risks and makes it easier for the rCB industry to attract investments and speed the adoption of its sustainable feedstocks
Collaboration not only increases the pace of innovation but also increases a crucial variable in the economy: demand. By collaborating, it’s possible to show more (tested and standardised) applications for innovative sustainable raw materials like rCB. This increases the industry demand not only due to regulatory restrictions on virgin carbon usage but also when it comes to the adoption of innovative technology. Additionally, increased demand brings more funding to the industry—allowing collaboration between R&D teams and investors.
By voicing our demand, we can bring more funding to the industry, increasing innovation and collaboration—and ultimately, improving circularity and sustainability. Each declared rCB kilotonne sold per annum matters. Every case study of successful, workable solutions lowers investment risks and makes it easier for the rCB industry to attract investments and speed the adoption of its sustainable feedstocks. Only by increasing industrial volumes can the rCB industry ensure quality and sustainability. By collaborating with investors, suppliers, and buyers, we can successfully decarbonise the tyre industry and get closer to meeting its environmental, social, and governance targets.
The opinions expressed here are those of the author and do not necessarily reflect the positions of Automotive World Ltd.
Krzysztof Wróblew is Chief Executive at Contec
The Automotive World Comment column is open to automotive industry decision makers and influencers. If you would like to contribute a Comment article, please contact [email protected]