The process behind painting vehicles is often a laborious task consuming many hours, sometimes days, between coats with masking usually being involved for more complex designs. With this in mind, leading digital technologies company, ABB Robotics, has developed a robot to assist with this task.
Equipped with 1,000 nozzles in the printed head the robot sees artwork and design tasks completed in less than 30 minutes. Named ‘PixelPaint’, this technology can be applied in a single coat and is opening the door to the personalised design market for the automotive industry.
We spoke to Joerg Reger, managing Director, ABB Business Line Automotive, Robotics & Discrete Automation to find out more.
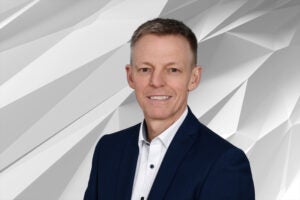
Just Auto (JA): Could you provide me with some background on your role and what it involves?
Joerg Reger (JR): I have overall responsibility for leading a team who support both leading automotive manufacturers and a wide range of major Tier 1 businesses.
We have a strong presence in all the major automotive manufacturing markets and whilst ABB is renowned for our line-side automation, our product portfolio and the range of solutions we offer has greatly expanded and will continue to do so.
This includes PixelPaint, our RobotStudio virtual commissioning software and with ASTI Mobile Robotics now being part of the ABB family, Autonomous Mobile Robots (AMRs) which are critical for improved intralogistics in automotive manufacturing. ABB also has pioneered the use of co-bots.
How does the PixelPaint technology work, what is the process for this?
Depending on customer requirements, ABB can supply PixelPaint with its IRB 5500 painting robot or with a high precision handling robot. Apart from the robot, the three basic elements of the PixelPaint system are the inkjet head, a dosing control package, and the programming software.
Of these, it is the pioneering inkjet nozzle design that makes it so capable. This incorporates 1,000 nozzles in just 100mm and droplets and can be applied in a variety of sizes ranging at a rate of over 1,000 droplets per second.
This enables precise control of paint film thickness and overlapping, ensures ultra-sharp definition of paint edges whilst eliminating paint wastage. The software package includes a user-friendly programming tool to enable offline programming for easy set-up and testing of two-tone and other complex paint applications.
How did the concept for this technology come about?
We had a series of in-depth discussions with a leading European manufacturer about the complexities they faced when applying paint designs to certain models.
The time required, availability of labour, logistical issues, high use of energy and the associated costs as well as the paint wasted in current processes were concerns. So, the question was raised as to whether a robotic solution from ABB could improve the process. That acted as the cue to begin a research and development programme and find the right solutions.
What are the key benefits of this technology when looking at client satisfaction as well as the automotive industry?
For the automotive industry, PixelPaint is designed to be deployed quickly and without requiring the levels of capital expenditure typically associated with introducing new paint processes.
Additionally, it acts as a time-saver for customers because even complex, bespoke designs can be completed quicker and without needing to move a car back and forth to the paint shop.
Multi-coloured car painting has traditionally been a laborious, costly process involving multiple stages of masking and unmasking, but this technology allows for a detailed, colourful, and exact replication of any design.
For the end customer, we believe it is all about extending choice and adding creativity. Ian Callum kindly contributed his own thoughts to a recent campaign we produced and underlined how the demand for even more personalization from customers is there and remains a key driver purchasing decisions. We should also add that there is an enjoyable and expressive element!
The solution claims to be environmentally friendly, how has it achieved this status?
The technology enhances manufacturing sustainability, removing the need for masking materials and extra ventilation, which lowers emissions while saving water and energy.
Coordinated by our RobotStudio software, the paint head tracks very closely to the vehicle body to ensure 100% of the paint is applied to the car with no airborne misting.
Different paint colours are applied quickly, with the product only running through the paint shop once. For car manufacturers, this can halve the production time and reduce costs by up to 60%.
Are there plans for future development with this type of technology for the automotive industry?
The potential for the product to develop even further is undoubtedly there and we will be closely listening to customers and understanding their requirements.
In particular, we are examining ways in which we can paint the entire body which would be revolutionary in terms of speed, cost-saving and sustainability.