Automotive supply chains are among the most complex in the world, writes Mike Short
Automotive companies around the world are moving production operations closer to their key markets. This not only gives them closer access to those markets, but it also addresses some of the top supply chain challenges that they’ve faced in recent years, like record-high shipping costs and long dwell times at ports.
In North America, Mexico is seeing a flurry of new automotive manufacturing activity, especially as the industry shifts to electric vehicles. The National Association of Auto Transport in Mexico expects to grow 20% in the next four years because of nearshoring efforts. Similar activity is happening in Europe, as companies eye countries like Poland, Hungary and Romania as closer production alternatives.
Whether an automotive company is moving a line or building a new plant close to a key market, they have a lot to consider from a supply chain perspective. For starters, they need to be sure the move makes financial sense. Also, no country is a cure-all for supply chain challenges. Each presents its own unique obstacles in areas like customs, transportation and cargo risks. Companies need to understand these challenges and have a plan for addressing them.
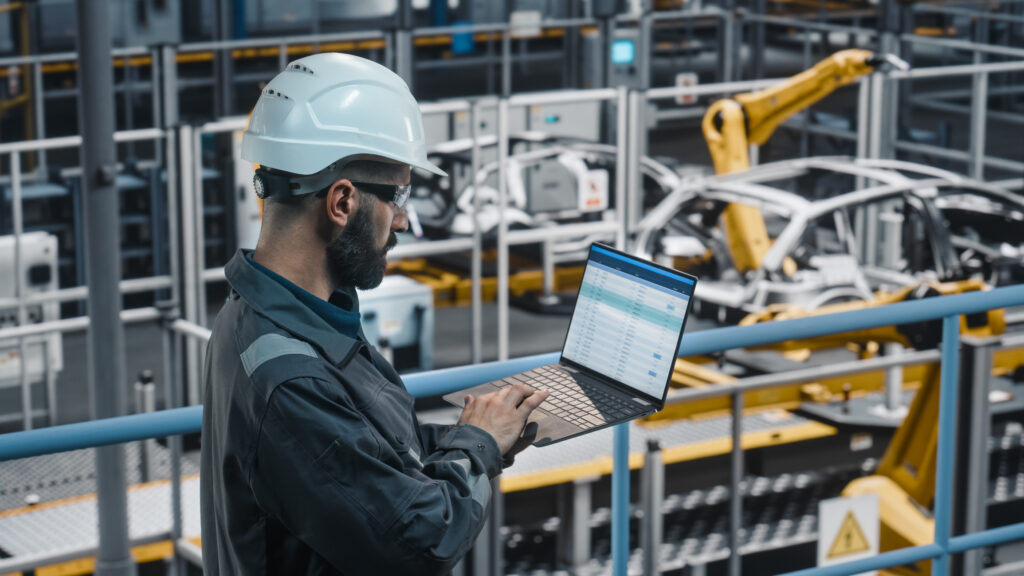
Companies that want to get the most out of their nearshoring activities shouldn’t think of them as just an extension of how they operate today. Rather, they should see nearshoring—and the reduced volatility in today’s supply chain—as an opportunity to take a fresh look at how they’ve designed their supply chain programmes and see where they can improve.
The cost factor
The bottom line is top of mind for automotive supply chain professionals after years of pandemic-related challenges. Port-to-port shipping rates increased severalfold from 2020 to 2022. On top of that, high detention and demurrage fees became a cost of doing business as cargo sat at congested ports week after week.
Expedited freight helped keep supply chains moving, but it also came with all-time-high air-freight costs. And as automotive companies tried to get ahead of supply chain disruptions, they ended up with higher inventory and carrying costs. Nearshoring can help companies recoup some of the higher costs that they’ve experienced over the last few years. But it’s still important that companies do their homework to confirm what savings, if any, they can expect to realise from a nearshoring project.
An automaker that plans to build a plant in Mexico instead of China, for example, will have some financial incentives. They won’t need to worry about paying the Section 301 tariffs or duties that they pay on shipments from China. At the same time, as ocean rates have gone down, these costs have become more manageable. So, they need to consider if shipping will actually be cheaper.
An automaker can also take advantage of USMCA, but they need to make sure they meet the agreement’s requirements in order to realise those savings.
No country is a cure-all for supply chain challenges. Each presents its own unique obstacles
All of this is why it’s important for supply chain professionals to look holistically at the costs of their nearshoring project. First, they need to determine the cost of manufacturing a product at a certain location. Then, they can identify their transportation costs and potential duty and taxes, while making sure they do indeed qualify for incentives like those available from free-trade acts. They should also account for overhead and inventory costs. For example, what costs need to be covered for a product that takes five weeks to ship via ocean from China versus five days to ship over land from Mexico?
Optimising a nearshoring supply chain
A nearshoring project can have a significant impact on an automotive company’s supply chain. If a company is relocating a production line from one part of the world to another, for instance, it will need to rebuild the line’s supplier base from scratch. That’s a lot of work considering that tens of thousands of SKUs go into one passenger vehicle.
A sourcing analysis reporting service can help bring some clarity to this activity. It can help a company identify sourcing locations that carry trade agreements or other preference legislation that can help reduce their landed costs. It can also help a company understand how their sourcing programme compares to others and identify if there have been shifts in sourcing locations in their industry.
Relocating a production line can also involve a lot of logistics when it comes to disassembling a line, shipping it halfway around the world and then reassembling it at a new site. Most automotive companies don’t have experience in this area. That’s why some turn to logistics companies that not only have done the physical disassembly and reassembly work but can also use carrier relationships to get the equipment to the new site on schedule and identify cost saving options through shipping mode and lane diversification.
It’s also important to understand and plan for the customs processes and fees that are unique to each country. In Mexico, for example, every truck that crosses into the US is transloaded and goes through a full inspection. A customs broker can help a company prepare for these challenges and make the process more efficient with solutions like warehouse and transload services.
A new country can also introduce new risks into an automotive company’s supply chain. The physical security of automotive cargo, for instance, is a bigger concern in certain regions. Real-time shipment tracking and being able to use diversified routes and multiple border-crossing locations can help companies manage these risks and protect their shipments.
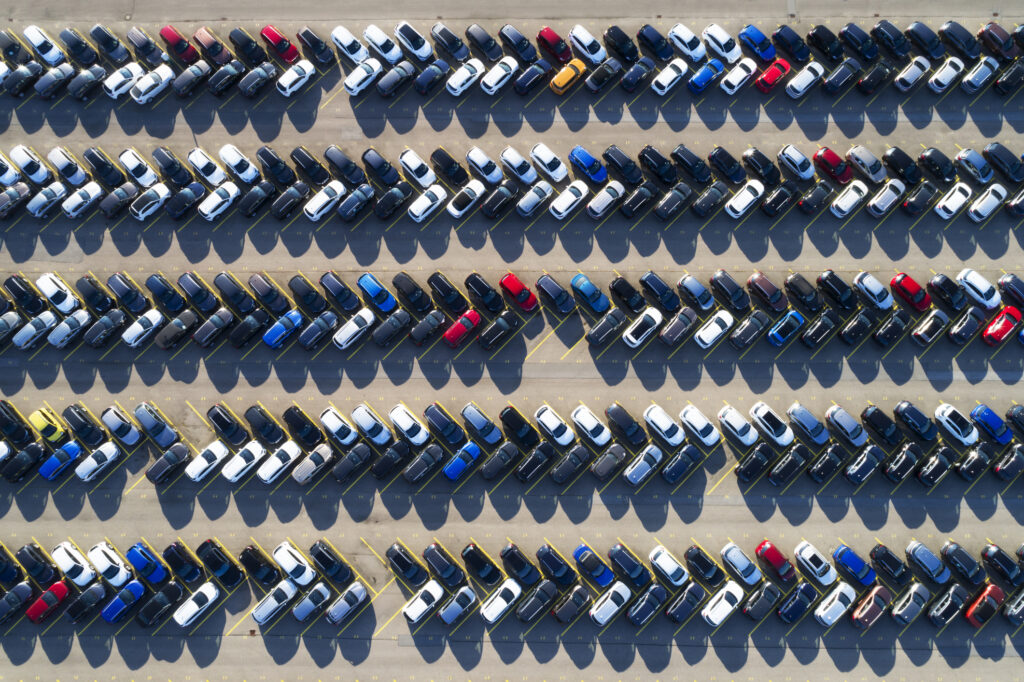
Harnessing data
Automotive supply chains are among the most complex supply chains in the world. And the pandemic helped highlight how volatile they can be because of all the potential for disruption. To help reduce this volatility for a new or relocated production site, companies should harness the power of their supply chain data. Real-time insights can help them see what’s happening in their supply chain and get in front of issues before they turn into disruptions.
For example, plan-for-every-part data is common SAP data. And an automaker can use it to know everything about every part— from where it was purchased to where it was used. This can help the company better forecast and ship against demand. Basic historical data like ship date and container weight can also help a company know if it’s shipping cargo in an optimal manner and best utilising each shipping container.
In Europe, it’s common for suppliers to use consolidation by shipping their products to a NVO (non-vessel operating carrier) operated consolidation centre. The goal is to build and ship full containers from the consolidation centre. But in recent years, containers being shipped out are often only partially full. This can be due to a variety of reasons like a supplier being delayed or specific components that can’t be stacked in a container.
Automotive supply chains are among the most complex supply chains in the world
At a new or relocated plant, a company can avoid this problem by using data to get a more holistic view of consolidation activities. They may see, for instance, that pooling certain suppliers together will help them more predictably fill containers to capacity. And they may see that certain suppliers simply aren’t a good fit for consolidation and recommend another option, like less-than-truckload (LTL) or less-than-container-load (LCL) ocean shipping, which many companies have taken advantage of.
Nearshoring in a new era
Nearshoring can give automotive companies relief from the economical, logistical and geopolitical complications that have disrupted their supply chains in recent years. But no region is free from disruptions and high costs. By dropping pre-pandemic thinking and embracing modern supply chain strategies—like using data to drive decisions and using diverse shipping options to remain flexible—companies can relocate their operations with minimal costs, risks and surprises.
About the author: Mike Short is President, Global Forwarding at C.H. Robinson