Switching to electric buses shouldn’t hurt a fleet’s bottom line, argues Miguel Simão
Climate credentials are no longer a ‘nice to have’ but rather an essential element for many companies. Combine this with ambitious targets of reducing greenhouse emissions by 55% by 2030 with the European Green Deal and the EU’s proposition to ban sales of all internal combustion engine (ICE) vehicles from 2035 and it’s clear that shifting to electric vehicles (EVs) has never been higher in the priorities of fleet operators.
Moving towards electrification is no longer something that only large public transport fleets do; providers of all sizes will have to make the shift within the next few years to ensure business continuity. With electric bus sales across the EU forecasted to grow by 83% in the next two decades, fleet operators need to take action now to get a better strategic understanding of the EV transition and the long-term impact on their bottom line.
However, EVs are a relatively new technology, and the upfront cost of an electric bus is still significantly higher than that of an ICE model. Furthermore, fleet managers are faced with the challenge of computing the life cycle costs of purchasing an electric bus and laying out the case for making the initial investment. As a result, the challenge for fleet operators is twofold. How can fleet managers and the transport industry gain a strategic understanding of the EV transition to help them to switch?
Predictive maintenance for economic viability
There is no doubt that transitioning to a fully electric fleet requires twice the investment when compared to standard ICE vehicles. However, electricity costs a fraction of fossil fuels, significantly reducing the operational costs. In order to capitalise on the lower energy costs and ensure a positive ROI, transportation services will need to operate vehicles for longer periods and more intensively when compared to traditional fleets. Utilising predictive maintenance in this process is a critical element to keep vehicles out of the workshop and on the road, enabling the economic viability that is needed for zero-emission vehicles’ mainstream adoption.
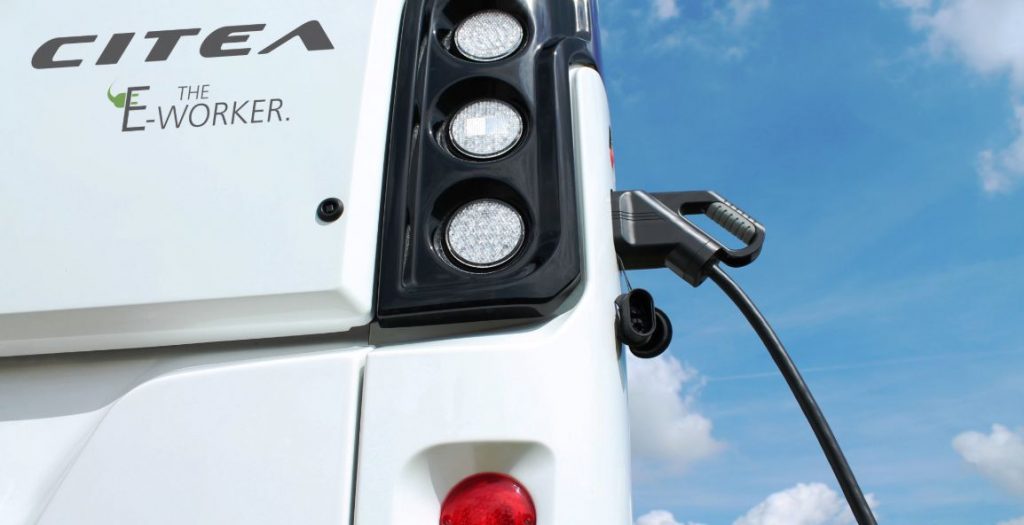
An electric bus has fewer moving parts, and these parts typically have longer life cycles, which significantly reduces the need for recurring maintenance. However, labour and components are generally more expensive in EVs, which means there are significant gains to be had in increasing their life as much as possible. Batteries are by far the most expensive component of electric buses, accounting for an average of 40% of the cost of the vehicle. For this reason, public transport fleet operators looking to make a profitable shift to electric fleets must consider how they plan to extend the life cycle of their vehicles’ batteries.
Much like smartphones, battery life decreases over the years and the range of electric buses becomes shorter over time. Manufacturers have tools at their disposal to extend battery life, such as thermal management and voltage limiting, but even then an EV that has a maximum range of 300km when new and only needs one charge to complete its daily route may require an additional charging session to complete the same distance after a few years. Additionally, the maximum distance the vehicle can travel on one charge may vary due to uncontrollable factors such as weather, traffic, route and vehicle load. The fleet manager must understand the limitations of their vehicles and the impact of these factors in order to avoid decreasing the service level.
Traditionally, vehicle maintenance is performed preventively, at estimated intervals. Sometimes components are replaced before their end-of-life, and other times breakdowns occur unexpectedly, causing service disruptions. Fleet managers reduce expensive breakdowns by replacing components at shorter intervals than needed. But this is an inefficient process as more parts are replaced before the end of their operational life. This inefficiency can be tackled with predictive maintenance. The vehicle’s data, collected during regular operation, is used to estimate the true remaining useful life (RUL) of components. With this information, fleet operators can gain a strategic advantage by optimally scheduling vehicle servicing to extend the operational life of parts.
Embracing predictive maintenance technology will not only smooth the transition into EV technology but also sustainably spearhead fleet operators into the next generation of e-mobility
Predictive maintenance is even more impactful in EVs due to their higher component and labour costs. With this technology in place, maintenance is more predictable and less expensive. The number of breakdowns is minimised, thus preventing costly downtime and expensive, unplanned trips to the workshop. Simply put, by pushing down costs and improving reliability, public transport providers will be able to make their vehicles run for longer, serve more people, and secure a return on their investment.
Add in AI
Technologies like predictive fleet maintenance platforms that use AI to provide real-time, actionable insight into the internal faults of electric buses allow maintenance managers to diagnose malfunctions remotely, without having to recall a vehicle off the road and physically look into it. An entire fleet can be monitored remotely, at any time and from anywhere.
The combination of large-scale processing, autonomous AI systems, and granular collection of vehicle data allow maintenance teams to fully leverage the data under the hood. The integration of AI solutions with connected vehicles and workshop information results in a feedback loop that feeds itself continuously and helps the system improve automatically during the fleet operation. This translates to higher quality failure prediction and continuous adaptation to new vehicles and automotive technologies.
In addition to the maintenance challenges of EVs, their limited range can cause logistical problems to public transport fleet operators who need to plan routes and consider the maximum range the vehicle can do and the availability of chargers along the route. One recent study completed by the University of Halmstad and Caetano Bus goes far in addressing this issue. Advanced data analytics and machine learning models were used to build a regression model that combines the battery data collected on-board the vehicle with other variables affecting vehicle range, and made it possible to accurately predict the present vehicle’s remaining range and the expected battery capacity loss over the next few years. The findings of the project have been implemented in a predictive maintenance solution in order to understand when the battery must be replaced or when the vehicle has to be operated with shorter routes. This provides public transport companies with the peace of mind of knowing with precision how their buses’ batteries are going to perform in one, two, or five years’ time. Fleet managers also benefit from an accurate prediction of the current range of the vehicle, calculated on the battery capacity and adjusted to account for the estimated capacity loss, as well as alerts for unexpected battery faults.
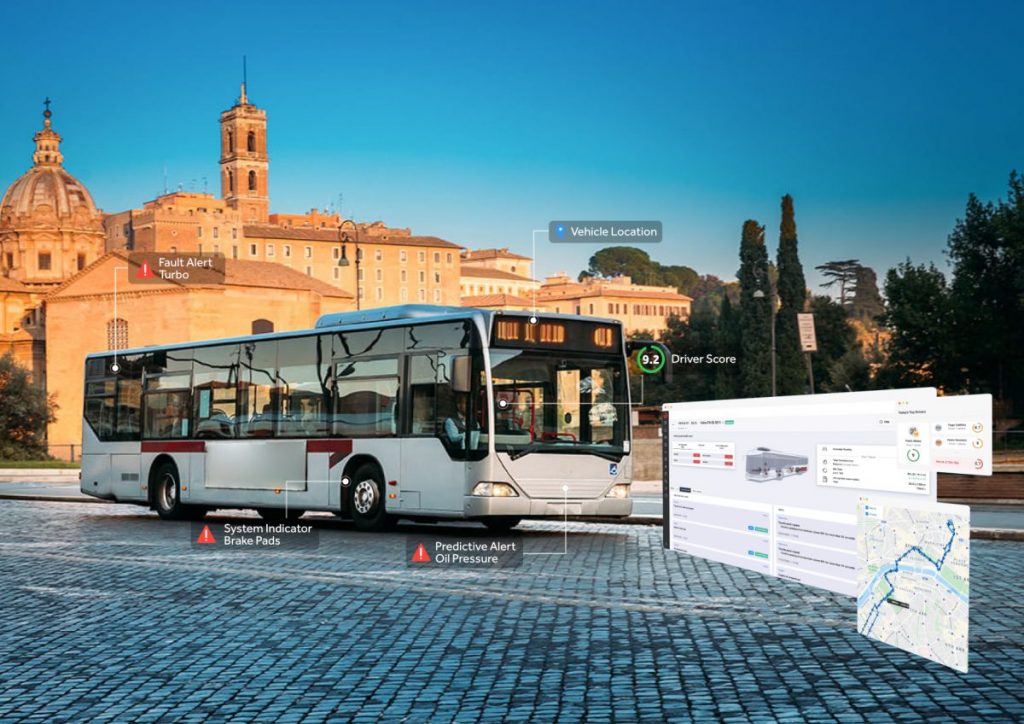
Mindful of the range losses in electric buses, public transport fleet operators may also make certain operational choices aimed at extending the battery life cycle and maintaining its capacity over time. Manufacturers offer guidelines on how to do that, but their main concern is to prevent excessive degradation during the warranty period. However, with proper usage, a battery should have a life that vastly exceeds the warranty period.
There are operational metrics targeted at extending battery life beyond warranty which should be monitored in real time within a platform, such as the State of Charge (SoC) optimality over time, i.e. the percentage of time spent at a healthy SoC range, typically between 20 and 80%. Another important metric is the Depth of Discharge (DoD), i.e. how much the battery is discharged between consecutive charges, which should be lower than 60% for maximum battery capacity retention. The fleet operator can visualise the SoC and DoD scores and understand if the operation profile can be changed to maximise battery life, reducing the total cost of ownership of electric buses. This type of analysis is fundamental for an operationally successful and profitable EV fleet deployment.
Smoothing the transition
Providing sustainable and accessible transportation which depends on the lowest possible cost per mile must be core to bus providers and their service offering. The lowest cost per mile can be achieved by extending the life of components, operating vehicles more intensively and for much longer hours while keeping them out of the workshop and on the road by eliminating downtime.
Empowering every fleet in the world with predictive maintenance to eliminate vehicle breakdowns and enabling reliable and on-time transportation services could save millions of people from the hassle of public transportation delays, postponed deliveries, or late arrival of essential goods due to the disruptions happening everyday caused by vehicle breakdowns and lack of visibility over a vehicles’ true condition. Embracing predictive maintenance technology will not only smooth the transition into EV technology but also sustainably spearhead fleet operators into the next generation of e-mobility.
About the author: Miguel Simão is Lead Data Scientist at Stratio Automotive