A new prismatic battery interconnect system helps to speed up battery pack production and cut material costs. By Randy Tan
Electric vehicle (EV) battery cells come in three fundamental formats: cylindrical, prismatic and pouch. In China, in particular, the prismatic cell format dominates with the new energy vehicle (NEV) OEMs. In addition, Tier 1 gigafactories support both the domestic market and major OEMs in Europe and North America. According to P&S Intelligence, globally more than 60% of battery cell types will be prismatic.
The existing prismatic cell assembly method relies on current collector assembly (CCA) technologies that, while matured, exhibit inherent inefficiencies. A significant challenge arises from the intricate, multi-step process involved in laminating and assembling the carrier, which includes low-voltage data collection circuits, current collectors, and terminal busbars. This process encompasses either moulding or thermoforming the plastic carrier and employing hot lamination for the CCA.
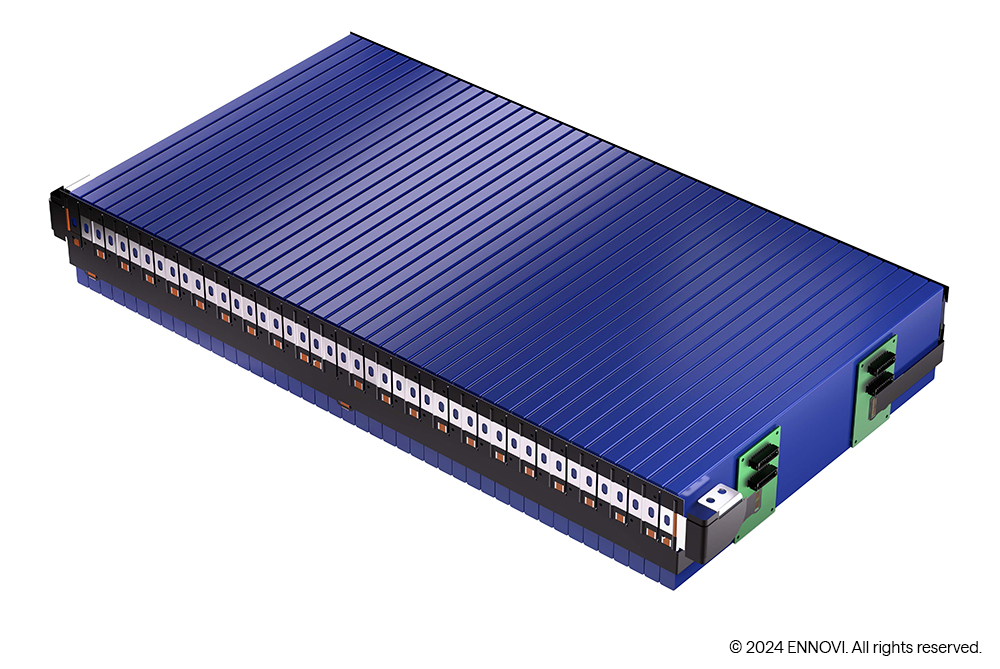
Introducing FDC as an FPC alternative
For the low voltage data collection media the predominant form uses a flexible printed circuit (FPC) made by a third-party supplier. The photolithographic process used to deposit copper onto the film and etch the material to leave copper traces on the FPC is a relatively slow batch process and the chemicals used are not environmentally friendly. There is also the issue of recycling the copper from the chemicals.
Within certain design criteria, the FPC can be replaced with a die cut circuit, known as FDC, which can be performed using a fast in-house process that is more cost-efficient. Taps extend from the copper traces for ultrasonic welding onto the aluminium current collector to monitor the voltage of each cell, replacing the need for additional nickel taps. Also, because the pre-laminated copper traces are die cut, the need for using etching chemicals is removed and the excess copper can be easily recycled.
Typically, the FPC uses PI insulation, which has a high thermal resistance, because the strategically placed electronic components, such as the two or three NTC sensors, are soldered onto the copper traces of the assembly afterwards at a high temperature. Instead, the FDC uses an automotive-grade PET material and the electronic components are attached using hot-bar soldering. This process uses a smaller header to focus the energy required to attach the components, minimising the heat flow without impacting the integrity of the PET.
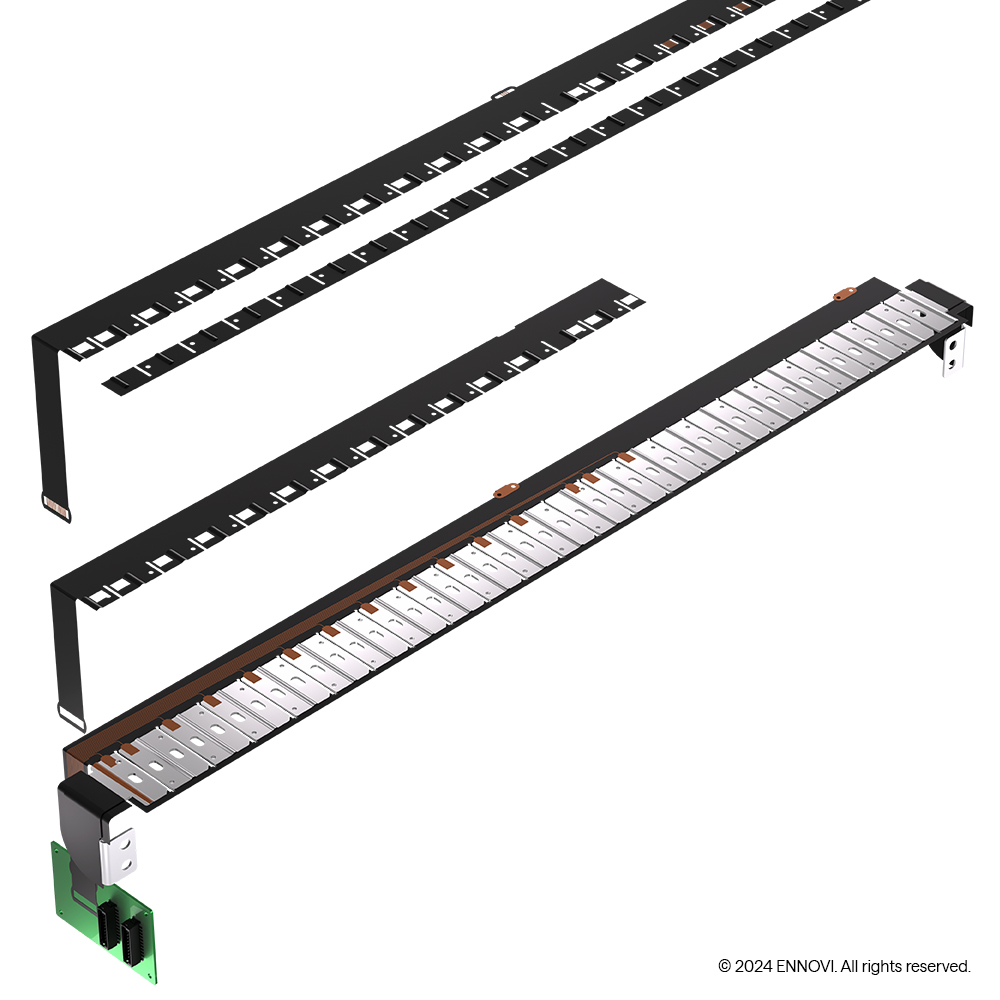
One-stop lamination
The middle and bottom PET layers have die cut copper traces pre-laminated, replacing the FPC from a third-party supplier. The top PET layer insulates the die cut traces, with additional PET layers for the aluminium current collector. Typically, the positive and negative terminal busbars are insulated using a powder coating, instead these are also laminated.
By optimising material usage and choice, bringing production in-house and combining a multi-step process into one, emerging battery interconnect systems will enable OEMs and gigafactories to scale and speed up their battery production without impacting overall reliability and safety. The one-stop lamination process also supports higher voltage (800V and above) designs for faster NEV charging times.
As well as prismatic cell formats, the flexible and highly customisable platform can also be used for cylindrical and pouch cell types. EV manufacturers are always exploring new concepts and technologies, like reducing the hot lamination cycle time or adopting cold lamination, which will reduce energy consumption and open further opportunities for OEMs and gigafactories to attain their sustainability goals.
About the author: Randy Tan is Product Portfolio Director at ENNOVI