Simulation allows engineers to see how motion control capabilities will behave in increasingly complex vehicle architectures. By Christophe Bianchi
Many of the greatest innovations and advancements in the automotive sector in the 21st century have been about improving performance and motion control in a vast range of vehicle models. The automotive industry has been focused on developing innovative electric and autonomous designs for years but there is certainly a heightened sense of urgency today. Meeting ambitious climate and safety targets means automotive development teams need to overcome some difficult engineering challenges, including more cost-effective battery designs, more efficient powertrains, and more robust electronics architecture.
But how can the dynamics of complex structural vehicles continue to evolve to keep up with an industry undergoing tremendous change? To move this exciting industry forwards, a mix of real-world testing and simulation is required to meet consumer demand.
Autonomous vehicles: the race towards a limitless potential
The development of autonomous vehicles is gathering pace. In the UK alone, self-driving vehicles are set to be worth nearly £42n (US$52bn) by 2035.
The task of motion planning and control of an autonomous vehicle is complex and challenging. Autonomous driving systems rely upon sensors and embedded software for localisation, perception, motion planning, and execution. Hands-off autonomous driving systems are mostly built and designed with algorithms that can be trained to make safe journeys. For motion planning in autonomous vehicles, there is global planning, which is the route planning from source to destination alongside local path planning. A combination of machine learning and deep learning is being used to by today’s top automotive engineers to implement a fully automated control loop. Essentially, the loop is comprised of motion planning (what behaviour the vehicle is planning), perception (what the vehicle observes), and motion execution (how the vehicle will complete the plan). This control loop is executed in a cyclic fashion so the vehicle can respond to constant environmental changes.
How can the dynamics of complex structural vehicles continue to evolve to keep up with an industry undergoing tremendous change?
This is defined by control logic, which is generated and coded to safety and security standards. This code is verified by engineers breaking down the overall vehicle architecture to guarantee safety for each of the components. To verify the safety of these complex algorithms used for perception, motion planning, and execution, simulation is used by engineers to arrange objects and events to simulate difficult cases that challenge both autonomous driving systems as well as human drivers. For example, graffiti on road signs can alter the reading of the system, often challenging perception. Simulation can test different variables and variations in deep learning models and scenarios with extensive content libraries that enable the creation of unlimited driving scenarios of virtual roads. Training these advanced driving systems algorithms requires extremely large sets of data that must be accurate and ‘true to physics’, and is generated by simulation leveraging access to immense resources from cloud computing.
Progressing from Level 3, to Level 4 and Level 5 autonomous driving will rely on the ability of the car to communicate with other vehicles and the infrastructure. It must be able to constantly do this with very low latency and with cyber security. The only way to achieve this is to simulate and validate through Digital Mission Engineering, an approach where the complete mission of vehicle within its complex environment is fully modelled with ‘true to physics’ accuracy on a very large set of scenario and edge cases.
The future of electrification
Worldwide sales of EVs are increasing rapidly, growing by 46% in 2020 and by 160% in the first half of 2021. Strategy Analytics predicts that 40% of all cars sold across the globe in 2027 will be electrified, rising to over 95% by 2050. EVs have the potential to impact energy, climate, and transport. This rapid change is coupled with increased demand for centralised networking architectures to power advanced control systems for vehicle dynamics and car motion. Electrification introduces significant engineering challenges that mix a large set of physics: behaviour, safety, and performance of EV batteries which combines electrochemical, thermal, electrical, electromagnetic, mechanical, and fluid (air or liquid cooling) physics that all interact with each other.
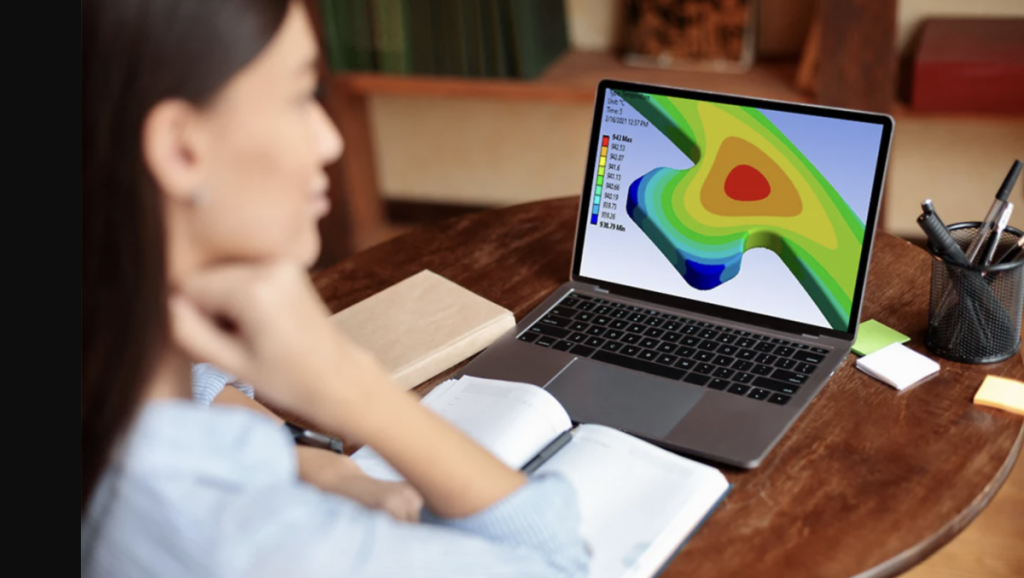
The recent emergence and fast-growing popularity of these vehicles requires performance control and consideration of the electric motor. In the production of EVs, key performance metrics include body design, energy system and optimising all components at a system level. For example, the motor drive system which consists of the motor, power converter, and control, is an essential aspect for engineers and designers as it has a significant impact on the performance of the vehicle. Due to EVs being a research priority in the industry, there have been advancements in machine learning, computer technologies and motor drive control engineering. Flexible and scalable software solutions will enable the next generation of leaner, greener cars to meet market demand.
Simulation as a superpower
Multi-physics simulation gives companies the ability to predict, analyse and explore how vehicles will work—or won’t work—in real world scenarios. Based on the fundamental principles of modelling, physics, mathematics and computer science, simulation gives engineers the power to see how motion control capabilities will behave. Perhaps even better, it reduces or even eliminates the need for costly physical testing.
For motion control improvements, simulation software allows designers and engineers to tap into millions of different test scenarios to run advance testing, within seconds. In the sphere of autonomous and electric vehicles there is an increasing focus to make design more efficient, powerful, and reliable, all whilst reducing overall vehicle weight and size. Sophisticated and complex engineering trade-offs therefore must be analysed—and at early design stages before development costs have been invested. If fully autonomous vehicles are to become a reality anytime soon, engineers need to take advantage of physics-based simulations and virtual reality simulations for autonomous vehicle testing.
We all want reliable, safe, innovative, and comfortable vehicles to perform our day-to-day activities, and many of us want the latest models in the autonomous and electric industry. Electronic vehicle control is skyrocketing in popularity, especially with the allure of self-driving vehicles and advanced driver assistance systems in EVs, and simulation will remain an essential tool in the push for future mobility.
About the author: Christophe Bianchi is Director of Business Strategy at Ansys