The introduction of 800v-compatible silicon carbide converters could define next-generation automotive inverter technology. By Jack Hunsley
Inverters are a critical part of the electric vehicle (EV) drivetrain. Put simply, their role is to convert a direct current (DC) supplied by the onboard battery in three separate phases; into an alternating current (AC) for the vehicle’s traction motor, back into DC to enable regenerative braking and, finally, to control motor speed when the accelerator is depressed. Without these inverters, EVs would not be able to function at all.
Playing such a vital role, it is no surprise that innovation around inverter technology is high on many stakeholders’ agendas. Mastering the next generation of this tech could prove a highly lucrative business.
Across the board gains
A key development area is 800-volt-compatible inverters. As the voltage suggests, these inverters are preparing for the arrival of more 800v EV batteries, such as that deployed in Porsche’s electric Taycan back in 2019. The technology is slowly nudging towards mass-market models, however, like Hyundai’s Ioniq 5. The automaker announced in December 2020 that it will transition towards an 800v-compatible modular architecture for its upcoming EV range, which will see 23 models released by 2025. The Ioniq 5 is the first in this collection, and a key selling point is the charging speed its 800v battery can cope with: via 200kW ultra-fast charging technology, the Ioniq 5 can be recharged from 10% to 80%, adding roughly 200 miles of range, in less than 18 minutes.
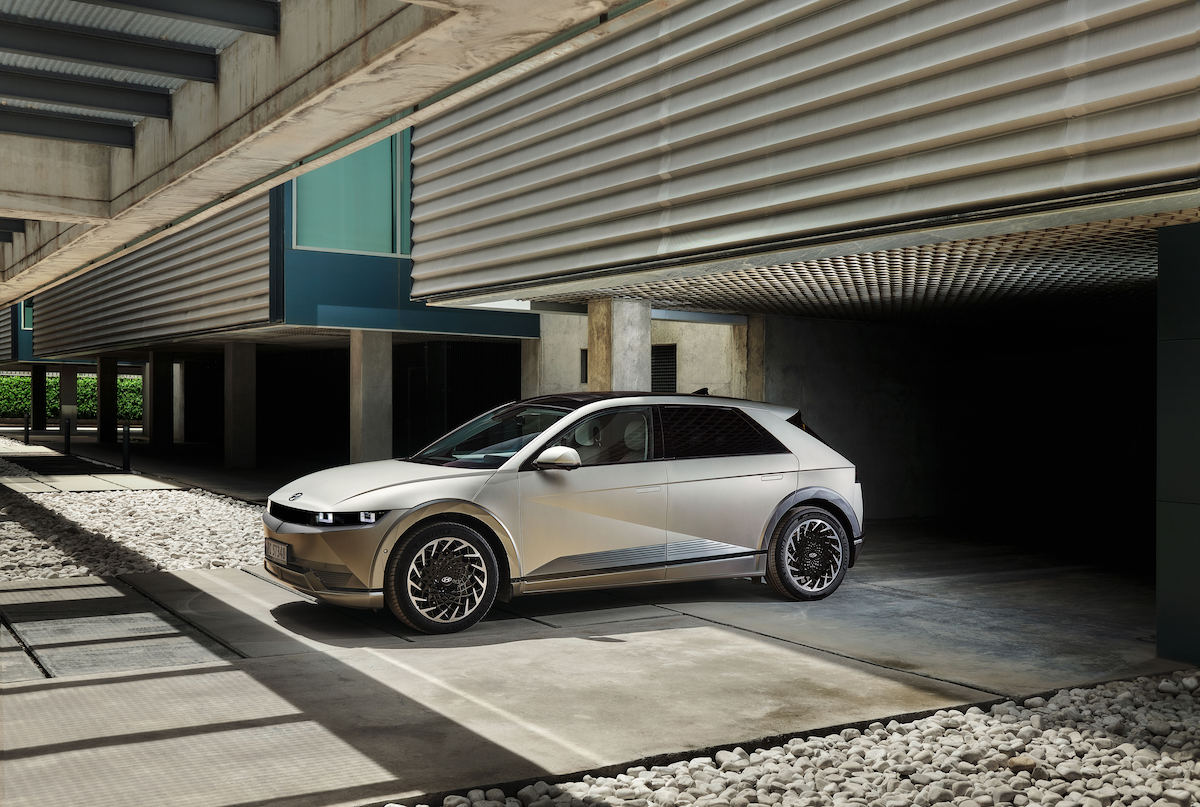
Such potential is seeing numerous players scramble to produce capable inverters. In March 2022, for instance, McLaren Applied offered the first glimpse of its upcoming 800v inverter. The manufacturer said that it is “advancing closer to full production” of its Inverter Platform Generation 5, which it claims will offer “class-leading efficiency and power density” courtesy of accelerated development enabled via the company’s Formula 1 effort.
Outlining the key gains, McLaren pointed to the inverter’s ability to support ultra-fast charging and the lighter electric cabling, which is expected to become a feature in next-generation EVs. Meanwhile, the use of silicon carbide (SiC) also allows for “the use of a faster, more efficient and lightweight drivetrain.” SiC offers an improvement on today’s commonly used silicon semiconductors as it produces less heat and is less temperature-sensitive. As such, by leveraging SiC, McLaren also claims to have created an inverter that can switch power more efficiently than conventional inverters, while also generating less heat to allow customers to use smaller cooling systems and reduce weight and cost by extension. Battery size can also be reduced by the same logic.
“Across the industry, we’re seeing rapid progress of technology,” said Nick Fry, Non-Executive Chairman of McLaren Applied, at the time. “If OEMs want to remain competitive and deliver vehicles with greater ranges, faster charging times and better acceleration, they must make the transition to an 800v SiC architecture.”
McLaren is not the only player to see great potential in 800v SiC inverters. In January 2022, Vitesco Technologies announced it had signed a deal with an as yet unnamed major North American automaker to supply 800v SiC inverters from 2025. The supplier says the deal is worth €1bn (US£1.08bn) which, in combination with its Q4 2021 sales across its entire electric component portfolio, will yield more than €2bn. This revenue also benefits from orders from unnamed Chinese and Japanese automakers.
“This is where the growth is happening and it’s also where there is real potential for the sustainable and increasingly carbon-neutral mobility of the future,” said Thomas Stierle, Head of Vitesco’s Electrification Technology business unit, speaking on the news. “The latest orders clearly prove the point. The electrification of automotive drive systems is progressing faster than ever.”
Quick development
The rapid progress in this space presents a huge logistical challenge for the industry. To simplify R&D processes, more companies may wish to consider bringing their inverter development in-house rather than relying on external suppliers. China’s Nio, for instance, announced in June 2021 that it had begun production of a C-sample prototype of an in-house designed SiC powertrain for its ET7 electric model. This route may prove attractive to players that want to integrate their powertrain development efforts more tightly within their organisations.
The speed at which the market is moving has sparked interest in solutions that can reduce inverter development time. For instance, during a recent Mobex webinar, Renesas Electronics detailed how it offers system-level functional safety support to allow its customer to shorten development time while producing inverter products. “Renesas can provide customers with a turn-key solution, equivalent to an A-Sample,” said Masashi Tsubota, Senior Principal Specialist at Renesas. “As a semiconductor manufacturer, we can design and support solutions that take full advantage of our ECUs and other devices.”
If OEMs want to remain competitive and deliver vehicles with greater ranges, faster charging times and better acceleration, they must make the transition to an 800v SiC architecture
On the theme of reducing development times, Drive System Design (DSD) also believes it has a helpful solution for this growing segment. It has developed what it calls the ‘Open Platform Inverter’ (OPI), a “highly customisable inverter hardware paired with flexible, modular and easily configurable plug and play software.” Though DSD remains an engineering consultancy with no plans to become a component supplier as such, the company’s Murray Edington, Head of Electrified Powertrain, told Automotive World that it sees an opportunity to help companies working on B and C sample inverters.
“We saw a need in our customer base for a rapid prototyping development inverter,” said Edington. “For customers whose core IP centres around novel motor technology, they would benefit from focusing on developing their business around that IP rather than handing a chunk of their investment to a third-party supplier. We can help customers avoid massive non-recurring engineering charges to access existing commercial inverter products as, for some businesses, non-these charges can be a significant hurdle.” By instead offering an open platform, DSD is confident it can play a key role in aiding future inverter development.
As for the inverter market as a whole, the consensus is that a shift towards SiC inverters is quickly arriving. The potential to improve charging and thermal efficiency and increased power all while reducing weight and costs means it provides an array of attractive benefits for OEMs beginning to release EVs built on dedicated e-mobility platforms. Expect an acceleration in the technology’s transition from deployment in supercars like the Taycan to mass market models.