John Miles explores how cloud technology is enabling a new wave of innovation within the automotive industry
The automotive industry is at a turning point. Bloomberg estimates that by 2040, 54% of new vehicle sales will be electric, and by 2030 100% of passenger vehicles in China and India will be electric. To keep up with this growth and evolving vehicle technologies, automotive manufacturers need connected, information-driven operations to produce vehicles as rapidly as possible, with the lowest possible cost and risk.
A window of opportunity
As EVs continue to rapidly transform auto production, established automakers and start-ups need to launch new plants or transform existing operations faster and smarter than ever before. Automakers must have the right EV strategy, centred around a shift to data-driven manufacturing in a highly flexible and connected environment, to stay competitive. While many manufacturers have been getting by with disparate and disconnected information systems running in the enterprise and across their facilities, that approach will not be able to keep up with the accelerated demand forecasted for the EV market. EV organisations should embrace cloud connectivity to achieve their long-term production and innovation goals.
Implementing cloud solutions can open the window to new opportunities for the modern enterprise, including greater visibility, reduced costs and increased productivity. Specifically, cloud-based systems allow manufacturers to gather real-time and accurate material and traceability data to make sure that production and delivery is always running smoothly. The cloud can also streamline operations to reduce the time it takes to make each product, decreasing downtime and minimizing waste. Lastly, the cloud enables manufacturers to shorten cycle times and improve efficiency by eliminating manual process errors with paperless operator control.
While many manufacturers have been getting by with disparate and disconnected information systems running in the enterprise and across their facilities, that approach will not be able to keep up with the accelerated demand forecasted for the EV market
The connected EV factory
Hybrid and all-electric vehicle production requires flexible and scalable operations. But what do flexible and scalable operations look like? They use analytics to help automakers stay efficient, even as powertrain technologies change. They use a manufacturing execution system (MES) to manage complexity, especially as production grows or evolves. And they use digital twin technology to simulate production changes before implementation, which help validate decisions and reduce risk associated with changes.
While the cloud in manufacturing is not meant to completely replace on-prem software, hardware and physical access, it provides new capabilities that expand upon existing systems to create efficiencies, improve collaboration and more. The cloud puts EV manufacturers “in the fast lane” by providing enhanced flexibility and efficiency to existing infrastructure and systems. And in an industry where every manufacturer is racing to be first, these time reductions make a difference.
Saleable analytics
Cloud transformation is especially beneficial for data collection and analytics because the automotive industry is no stranger to Big Data. Over the years, auto manufacturers have utilised smart cloud-based services and analytics platforms to aggregate, analyse and transform Big Data into powerful business intelligence. But despite advances, many manufacturers struggle to provide their operators with information that can drive real-time performance gains on the plant floor. This is due to gaps in closing control system loops between Big Data and the plant floor, typically caused by excessive network traffic and analytic lags.
Scalable analytics powered by the cloud presents a faster way to optimise information at the edge by closing the loop between Big Data and the plant floor faster. It embeds analytics and machine learning (ML) capabilities closest to the source of the information and plant-level decision makers. Using dynamic mathematical models, the system learns to recognise the impact one variable has on another and automatically adjusts subsequent actions for optimal results. At the same time, the system can deliver critical analytics to operators, such as SPC charts, which enable continual quality monitoring and proactive adjustments. This enables maintenance teams to make better decisions at the “source” of their data, minimising downtime and accelerating proactive decision making.
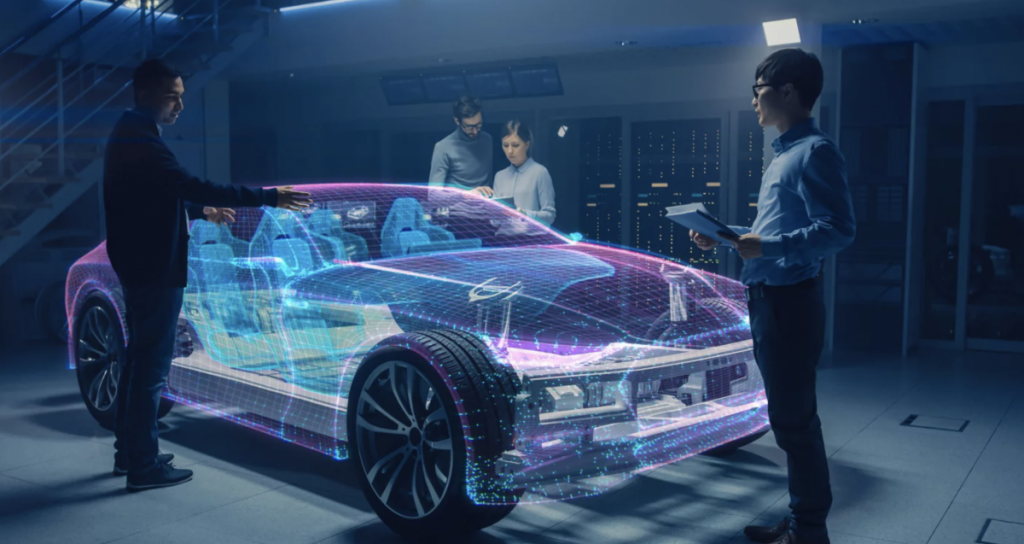
Digital twin
The growth of real-time data will also be the fuel for the emerging use of digital twin software. A digital twin is a virtual representation of a physical object. Digital twins in a cloud-based environment allow experts located anywhere to add useful insight into factory processes with ease. At the lowest level, digital twins can be a single machine, but they can also scale to represent a real-time digital counterpart of an entire EV production facility and the products produced. This tool can simulate new configurations and predict the impact of changes of processes in an EV plant, especially when housed in a cloud environment.
Digital twins are powerful in the EV space because of the flexibility they provide. They can help manufacturers shift to changes in production demand or revised specifications more quickly than ever before. As production processes evolve, for example, a digital twin allows manufacturers to test new products and configurations before they physically implement them and share findings with other members of their team to evaluate risk. Digital twins are also being used to keep track of components, software variations and updates over the lifetime of a vehicle as well as its digital twin. This information is then stored in the cloud and used for tracking and tracing across the connected supply chain.
Cloud-based MES
Automakers have long used MES solutions to improve agility, visibility, control access and throughput. These applications are beneficial for enforcing specified production processes and standards and they can coordinate activities throughout a plant to keep orders on track and assets performing optimally. However, many MES solutions are still deployed on premise, which presents hurdles in terms of streamlining operations and fostering collaboration.
The cloud puts EV manufacturers “in the fast lane” by providing enhanced flexibility and efficiency to existing infrastructure and systems
Cloud-hosted MES applications can address a manufacturer’s specific production challenges while also growing with their operations and their needs. A quality application, for instance, can track, identify and alert when a machine or operator’s processes go outside of their prescribed limits. Cloud-based MES is favoured among many EV manufacturers today because it provides them with everything they need to connect people, systems, machines and supply chains uniformly and at scale, enabling them to lead with precision, efficiency and agility.
While the EV industry has a solid grasp of its trajectory, implementing digital change in a fast and sustainable manner has proven challenging for many. Although Industry 4.0 and digital transformation were concepts that most EV manufacturers were aware of, there is a newfound realisation that embracing them may determine who thrives and who does not over the next several decades. Competing as a player in the booming EV market requires a manufacturing framework that delivers consistently refined and scalable process improvements that enable diverse things and systems to work together. To reach this level of adaptability, intelligent connected cloud technologies should be increasingly utilised. Reimagining automotive production in this way can help automakers and suppliers stay competitive in an unpredictable, yet auspicious, time.
About the author: John Miles is Global Head of Future Mobility, Rockwell Automation