Just when the auto industry was getting back on its feet, a global semiconductor supply issue threatens to wreck havoc, with both Ford and Mahindra already admitting to supply issues here in India too. With complex functions like ADAS and telematics, to even more mundane areas like headlights and mirrors, all digitised, microprocessors are increasingly in demand in automobiles today, and the shortage is proving to be a huge crippling factor.
The crash
The issue really all started in the second quarter of 2020 where, due to COVID-19, automakers around the world drastically reduced their production and thus component orders too. At the same time, chipmakers – who were also struggling with their own COVID- 19-related production issues – saw a spurt in orders from electronics companies like laptop, phone and even gaming console makers who all experienced a surge in business during the pandemic, thanks to changing work and school patterns.
The final nail in the coffin, however, was the much faster than expected recovery in auto sales, the Semiconductor Industry Association (SIA) said “the shortage is largely the result of substantial swings in demand due to the pandemic” and indeed, if one looks at the chart, it’s clear that not only was the recovery very quick, but the sale of auto chips climbed to even higher levels in Q4 than they were at the beginning of the year.
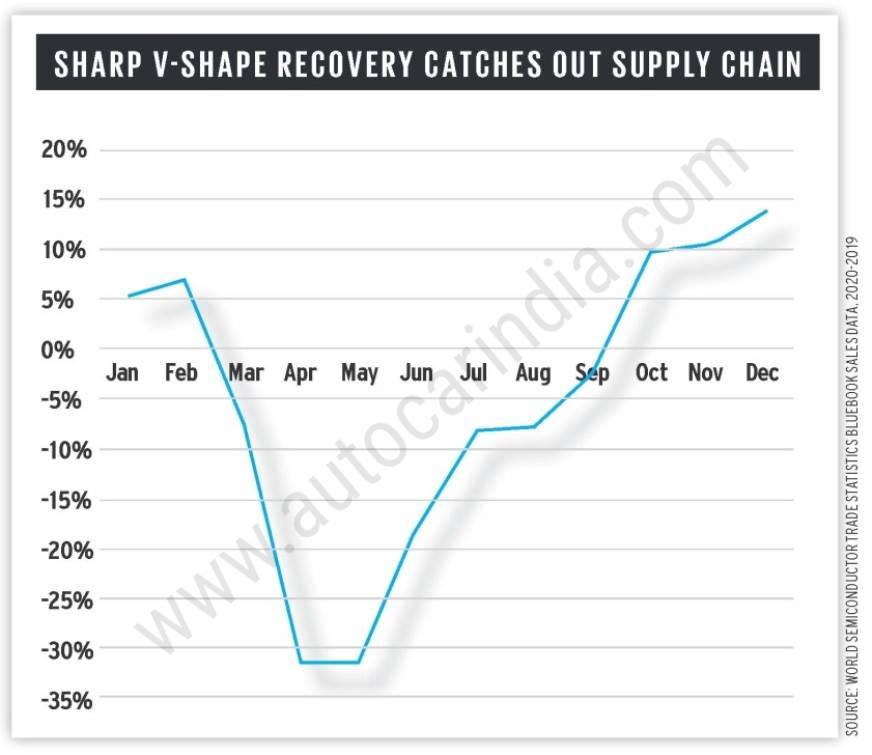
The exact impact on the industry is hard to pinpoint, however data analytics and consulting firm GlobalData estimates, “vehicle maker downtime announcements add up to around a 4,00,000-unit loss from forecast Q1 global vehicle production, but the opportunity cost – if the companies were producing to full capacity – is some 7,15,000. This leaves the Q1 revenue hit for the industry between USD 12 billion and USD 22 billion.”
Wafer thin
Making a chip is a very complicated process and the manufacture of the silicon wafer – the substrate upon which the chip circuits are built – is a delicate process relying on elements that are not easy to source quickly. Ford, via a statement, also indicated that the wafer foundries had not invested enough over the previous few years to increase capacities to meet ever-increasing demands. This is one of the reasons why chip manufacturing requires a lead time of at least 26 weeks.
Silicon industry experts further say the problem runs deeper and lay the blame with an industry that did not grow in a very structured manner. For one, there is an over reliance on few manufacturing facilities, and even fewer suppliers for machines and raw material too. Furthermore, semiconductor manufacturing has seen a very lopsided development in manufacturing capability, with countries around the world receiving very differing levels of government support, China – historically small players – are now rapidly trying to be major players with massive government support and thus mopping up global resources rapidly. For instance, the SIA says that in the year 2000 to 2020 Chinese chip makers received nearly 50 billion dollars in subsidies, compared to 0.5 billion that Taiwan doled out and zero for US makers. Interestingly, the US used to be a leader in semiconductor manufacturing, with a 37 percent share in 1990 but only accounts for 12 percent today. Chip manufacturing is now heavily dependent on countries in Asia like Taiwan and South Korea, where even US companies now outsource to.
Booting up
The SIA has said that it is “working diligently to ramp up production to meet renewed demand”, and earlier this month in a letter to US President, Joe Biden, urged the US government to “include in your recovery and infrastructure plan substantial funding for incentives for semiconductor manufacturing, in the form of grants and/or tax credits, and for basic and applied semiconductor research.”
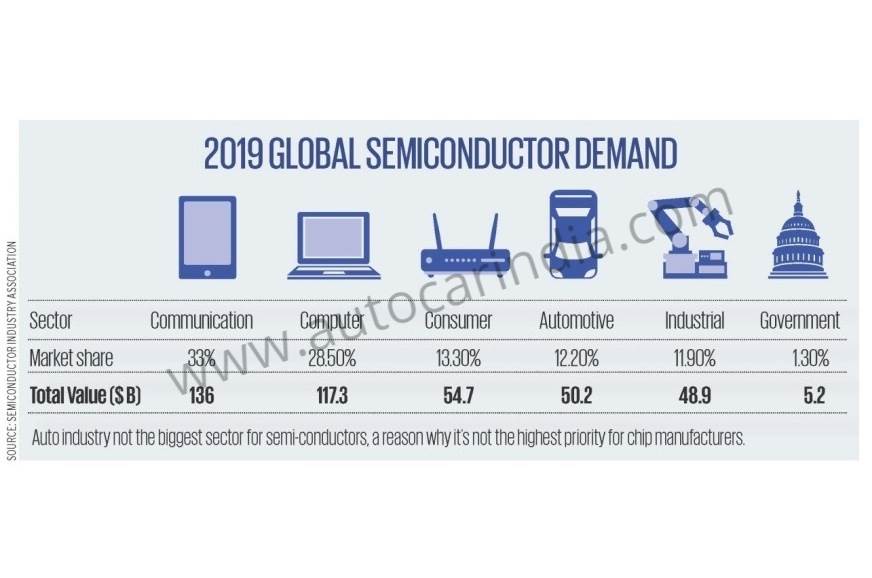
Having already had to shutter production plants around the world, automakers are as yet cautious. In the US, major automakers like Ford, GM, FCA, Toyota, VW and Honda, have all cut production and, in some cases, even shut it completely. In Europe too, German automakers, as well as brands like Ford and Honda, have also faced production issues.
A Volkswagen spokesman told our sister publication Autocar UK, “We haven’t quantified the full volume impact as we continue to work intensively with our suppliers to minimise shortages. However, we expect the ramifications to continue at least in the first quarter, with potential to recover any lost volume later in the year. Another issue we’re dealing with is the second wave of the COVID-19 pandemic and how it’s affecting not just our manufacturing operations but also the crucially important supply chain.” Thus, as things stand, with the world’s COVID-19 situation still volatile and causing disruptions to consumer demand, the semiconductor issue will take some time to finally settle down.
Issues back home
Ford
The American carmaker has had to shut production for a while. In a statement, the company said that both of its plants in Chennai and Gujarat are facing supply issues, and they expect shortage to continue through at least the first-half of 2021.
Mahindra
We understand that the issue is threatening to delay the launch of the Mahindra XUV500 as well as the new Scorpio, with Rajesh Jejurikar, executive director, auto and farm sectors, M&M, saying, “Anything around semiconductors is the primary supply chain constraint at the moment.”
Maruti and Hyundai
Larger scale manufacturers like Maruti and Hyundai have not released any official statement but their production remains largely unaffected. With a large product portfolio and carrying many similarities and shared components, insiders say they are better able to adjust the production of individual models to suit demand and mitigate the chip shortage issue.
The supply constraint has also caused some disruption at Tata Motors Commercial Vehicles.
Bajaj Auto
Premium bikes have been hit, Rajiv Bajaj, MD, Bajaj Auto said, “We are growing at over 50 percent but still losing production due to supply chain problems. This month we will lose, between domestic and exports, 6,000 KTMs because of shortage of semiconductors and ABS parts from Bosch.”