Defect rates could reach 30% during the ramp-up phase of EU gigafactories, but the Battwin Project proposes digital twins as a solution. By Stewart Burnett
If legacy automakers in Europe are to defend their business against insurgent Chinese electric vehicle (EV) brands successfully, battery production must be scaled dramatically. According to May 2024 estimates by the International Energy Agency, there remains an overwhelming disparity between East and West in terms of production capacity: whereas China accounts for more than 80% of global capacity, the EU and US only account for around 5% each.
As such, most Western automakers still rely on China for the majority of their EV batteries. However, there are many potential benefits for those looking to onshore, including greater supply chain resilience, transparency, and a significantly lower carbon footprint. While some emissions could be reduced by shortening trade routes, a greater amount could come from production itself. Transport & Environment estimated in May 2024 that onshoring to Europe would cut the emissions of battery production by 37%, rising to more than 60% when using renewable electricity.
Realising the scales required for electrification entirely domestically will prove a steep challenge. The EU projects that as many as 30 million EVs will be on European roads by 2030—a near tenfold increase from 2024. Meeting this demand will mean more than just the construction of gigafactories but also significant efforts to facilitate manufacturing efficiency and scrap reduction.
This is what pan-European energy transformation initiative, the Battwin Project, aims to achieve. Comprised of various partners across the public and private sectors, the project aims to develop a multi-level digital twin platform that will reduce defect rates in lithium-ion battery production. It warns that such defects could reach up to 30% during the ramp-up phase of Europe’s new gigafactories.
Facilitating mass production
“The big challenge we are collectively facing is meeting net zero targets and accomplishing a full transition to EVs and other zero-emission powertrains,” states Daniela Fontana, Electrification Solutions Development Manager at Comau. “For us, this means providing the technologies and solutions that will speed up the development, manufacture, and deployment of EV batteries.”
Comau, an automation technology firm that is part of Stellantis Group, joined the Battwin Project in April 2024. The company works with other Battwin partners to identify and define crucial data parameters, hardware, software, and digitalisation technologies that can feasibly be used to usher in defect-free battery production. Once this has been accomplished, it will leverage its in-house expertise around digitalisation to articulate and subsequently implement a multi-sensor data acquisition and management strategy that improves manufacturing quality.
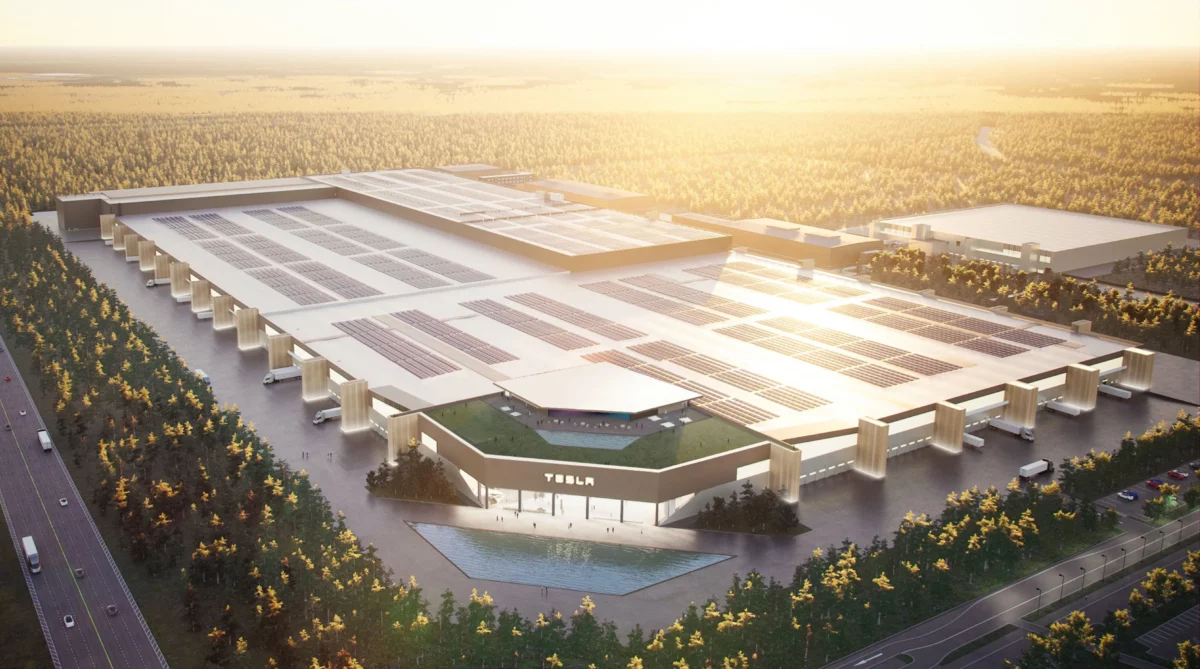
“A 30% defect rate is a big problem and equates to a large amount of wasted materials and production capacity,” remarks Fontana. In effect, this means that gigafactories will fall short of realising their stated capacity by a large margin while also creating needless and counterproductive industrial waste along the way. Although he does not provide names, Fontana states that OEMs have indicated their concerns to Battwin about these issues. “For them, the main drivers are quality and the reduction of scrap waste. So, we need to reverse these trends, and that in turn will reduce costs.”
Digitised factories
The first and most important step towards ensuring that Europe’s gigafactories operate at maximum efficiency occurs during the design and development stages. “The start-up phase is the most critical for reducing the defect rate,” says Fontana. The Battwin Project aims to implement tools and processes that facilitate smart decision making around the way in which gigafactories operate. This begins through the introduction of a representative, system-level digital twin model of the entire factory during the design phase. Issues like bottlenecks can be identified and addressed early on through simulations.
One way this will be accomplished is through discrete event simulation modelling. This allows battery manufacturers to test their planned production methods against potential disruptions and issues in a simulated environment. This approach can also be repeated during the factory’s operational stage as data from real-world production is fed continuously into the model. Digital twinning will also be implemented at the process level, modelling the critical stages of electrode manufacturing, cell assembly and conditioning through the use of multi-physics, data-driven, and hybridised approaches. Finally, the digital twins will be augmented with goal-oriented workflows that increase the explainability of data derived from them, making it easier for users to design and assert control over manufacturing processes.
“We want to cover all the different levels that are related to data analysis,” remarks Fontana. “This starts with the acquisition of data from the factory floor, which is then transmitted to the cloud, where it can be elaborated into twin models. The results of these simulations then provide feedback to the factory floor on how to improve decision making and optimise manufacturing.”
Fontana also highlights the potential for simulation models to address concerns around energy efficiency and gigafactories’ carbon footprints. Beyond the implementation of renewable energy sources, new processes could be developed that do not use toxic materials or reduce the amounts of solvents required in battery production. Various initiatives in both industry and academia are currently working in this vein, the results of which could subsequently be tested, validated, and implemented through digital twins.
Integration is key
As part of a wider European initiative to realise domestic battery production at scale, the Battwin Project will integrate with other continental efforts to facilitate battery production. One of the most important in this regard is battery passports, which are slated to go into effect from February 2027. These will be used to facilitate semantic and cryptographic verification of certificates and claims, thereby ensuring the integrity of data used in both factory and process-level digital twin models.
The start-up phase is the most critical for reducing the defect rate
“Solutions like ours will play a big role in meeting targets and ensuring data traceability. This will be especially important when battery passports are brought into effect,” says Fontana. Battery passports are themselves digital twins that store information about a battery’s production, including its lifecycle emissions from raw material sourcing through to manufacturing and eventual use.
The Battwin Project will conclude in June 2027 following 42 months of collaborative efforts. Ultimately, by realising its ambitions of creating multi-level digital twin models for all aspects of battery production, Comau believes it is entirely possible to reduce battery defects to near-zero. “If we can ensure less waste and higher quality, then European battery manufacturers will be better able to compete with Asian companies and meet the scale of domestic demand,” says Fontana.
This, in turn, will assuage concerns among some tentative EV consumers around battery reliability. If the EU is to meet its lofty electrification targets in 2030 and beyond, addressing such concerns will be essential.