Additive manufacturing is opening up new lines of business and supporting increased productivity. By Jordi Priu and Borja Batlle
Mobility has always been an industry of evolution, and the past 75 years have brought many advancements. More recently, COVID and its resulting supply chain challenges have supercharged the speed of change, and as a result, the automotive industry is moving at a more rapid pace than ever before.
Today, mobility is centred around energy and sustainability. While consumers and society continue to demand lower emissions, the electric vehicle (EV) industry will keep growing. However, we believe EVs will never make up more than 50-60% of the overall market. The infrastructure around EV is still not there, and it is only a matter of time until other sustainability ‘champions’ emerge, such as hydrogen-based technologies.
Unlocking additive manufacturing’s potential
To keep up with this trend of transformation and re-invention in mobility, suppliers need to be flexible and ready to meet the demanding timelines and budgets thrown at them by automotive OEMs. Technologies like additive manufacturing (AM) can help suppliers shorten lead times and keep up with the frequently changing manufacturing forecasts from the OEMs.
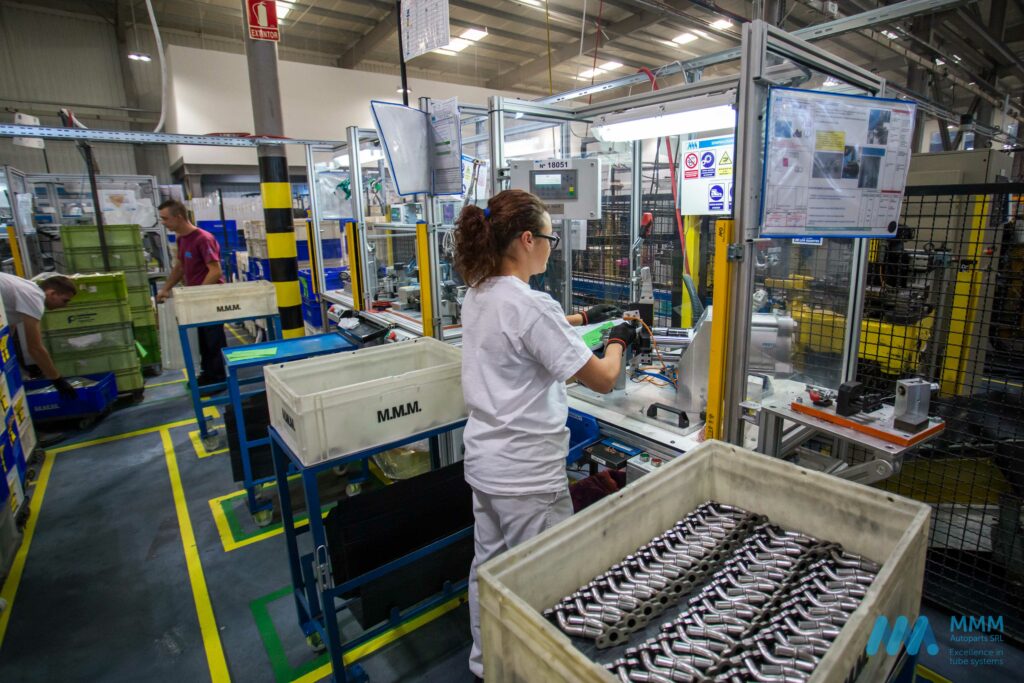
AM gives suppliers the opportunity to be as flexible as possible to meet theses changing market needs. It helps to accelerate processes, vastly cutting down component delivery time to weeks rather than months—and in some cases, even an on-demand. Having that ‘red button’ to push is a real selling point around the power of AM. Compatible simulation software also allows manufacturers to understand how their parts will perform inside an engine before they event print them.
Optimal applications for success
As with any technology, AM is better suited to some tasks than others. For example, we’ve found it ideally suited to producing jigs, tools, and other individual and highly specialised parts. Given its overall flexibility during the design and manufacturing process, AM can support a significant reduction in part development from start to finish. It also enables parts to be produced to check the quality, and fixtures can be designed and created without having to machine anything.
To ensure certain applications are well suited to the technology and that users are getting the most value from AM, it is essential to understand its challenges and limitations as well as its strengths. Ultimately, it needs to support the end goal—to be able to design, print, process and sell parts.
Ensuring 3D printed components and fixtures are the correct weight to pass a vibration test is one example of challenge that needs to be overcome to meet this aim. Designing new control tools and washers to help reduce the costs and timings associated with new projects is another. Being able to print and validate them to simulate assembly and mounting during production means companies can offer a real advantage—especially in cases where fixtures can be designed and printed in only a matter of a few weeks.
As an example, in our Romanian factory we produce a fixture for checking rubber sleeves. We used a Markforged X7 3D printer to create an internal mechanism inside the fixture with a worm gear. Thanks to the high-precision build, the fixture is able to check the maximum deviation of 1.0mm at the tube ends. This activity, which determines the precision for finding a part’s tolerance, has saved 60% of the total time for the cycle. Moreover, these sorts of mechanisms cannot be incorporated using traditional methods. It is only with composite fixtures produced using AM processes that these results are possible.
There is a great deal of value in helping customers identify the areas in their value chain where AM has the greatest potential. Engaging specialised engineering teams, coupled with the best additive manufacturing technology to analyse designs can help companies to achieve optimal results.
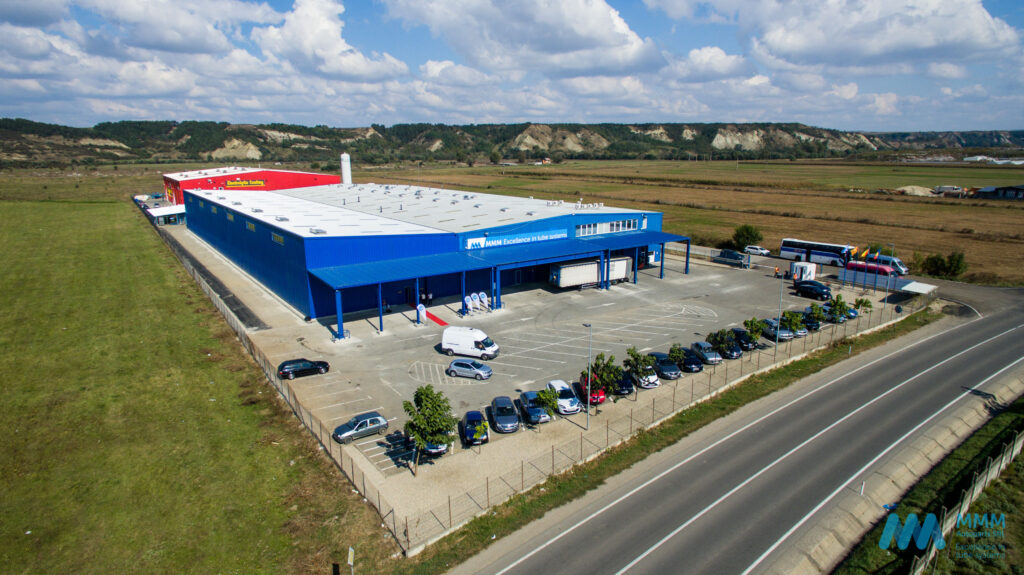
Finding the right partner
To complement fixture machining processes like the example described above, it is important to select the right AM partner. The hardware itself is only one part of the equation. It’s also important to find a printer that can create strong, lightweight parts using materials suitable for the automotive industry. Education is also essential, so finding a partner than can provide support as the company learns to create the right designs for the right applications, and enhance its understanding of the machine, the technology and what it can do, is pivotal.
Before deciding which provider to work with, it is also important to analyse the options and carry out tests. Ease of use, precision and versatility are all essential elements the right 3D printer should provide—as is its ability to reduce the end-to-end time for developing parts. Preventative maintenance should also remain top of mind when it comes to printing parts. The accuracy of the printing systems and specific DfAM (Design for Additive Manufacturing) strategies will always help to ensure strong results. including high precision rates with minimal deviations.
For Manufactura Moderna de Metales (MMM), it is ADDiVAL—together with Markforged—that ticked all of these boxes. Its X7 printer has proved to be versatile in helping produce high-precision and extremely strong parts in a short period of time. Originally, the printer was used to manufacture prototypes of components. Today, it is used to design and produce the final components directly in the factory, due to its ability to create continuous fibre reinforcement during the manufacturing process. We have also recently added the Metal X printer to our AM technology portfolio.
The future is here
When it comes to mobility, we find ourselves in a new era of innovation and implementation. The overall flexibility and precision of AM is opening up new lines of business, as well as helping to support increased productivity and part size for component manufacturers in the automotive sector.
While there is still progress to be made in accelerating the use of more sustainable materials, the industry is focused on making parts smaller, more efficient and with less waste. As such, we will continue to see new and specialised opportunities for AM across the globe. Manufacturers will not only build tools for internal use, but we’ll also see increasing volumes of parts being built on-demand for end-use applications, further accelerating the speed of change and innovation in an ever-evolving industry.
The opinions expressed here are those of the author and do not necessarily reflect the positions of Automotive World Ltd.
Jordi Priu is Chief Executive of Manufactura Moderna de Metales (MMM) and Borja Batlle is General Manager of ADDiVAL
The AutomotiveWorld.com Comment column is open to automotive industry decision makers and influencers. If you would like to contribute a Comment article, please contact [email protected]