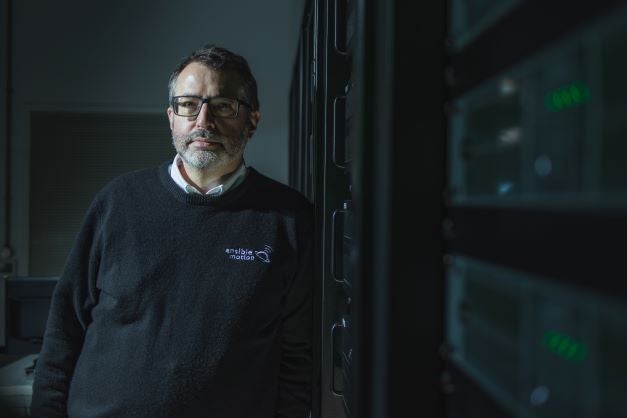
Ansible Motion has just revealed a new driving simulator. Can you tell us more about this and why you decided to create it?
There is a growing demand for high-fidelity, high-dynamic, human-centric vehicle simulations, and we wanted to create a versatile product that could be used by anyone who might benefit from a driver-in-the-loop (DIL) simulator. It’s no longer just chassis, performance, or HMI teams that are benefiting from DIL simulator technology, but also ride, ADAS, autonomy, V2X, ergonimics, powertrain and brand teams – and even legislative and regulatory bodies – that are finding answers and better solutions with our simulation offerings. In summary, I would describe the Delta series S3 as a turn-key virtual testing environment that provides everything necessary to convincingly connect real people with imagined vehicles and world spaces. Our aim with this design is to provide a useful tool for automotive product development, one that can be in use early and often to assist with exploring vehicle design decisions.
How is it different to the previous version?
With the Delta series S3, we took our original stratiform motion system concept and extended it to provide high fidelity, longer duration motions while keeping our trademark high-dynamic capabilities. We improved payload capacity, introduced simpler and stiffer dynamic load paths, and improved the kinematic design of the motion system. The results are high accelerations, high velocities, longer displacements with high bandwidth and precise motions at lower velocities for smooth reproduction of subtle vehicle attributes. It delivers accelerations beyond 1G, velocities above 5m/s and class-leading frequency response. We’ve also increased its turning capability for full 360° dynamic yaw rotations and our panoramic vision systems now match this with a large full-wrap projection. All these new attributes make the Delta series S3 perfect for real-world scenarios as diverse as aggressive lane changing, autonomous parking, AEB interaction, and many more. A number of key driving manoeuvres can be conducted 1-to-1 in terms of motion with the real world, providing unparalleled realism for a simulation environment.
Have you sold any?
Yes, in a very short space of time, the Delta series S3 has already become our most successful product to date. We have confirmed sales to Honda R&D Company, Continental, BMW, Deakin University in Australia, together with several other projects I can’t name.
What is convincing them to buy your simulator?
A number of factors. First, driver-in-the-loop simulation is all we do and all our resources and R&D is poured into that, without distractions. I believe we also deliver on our promises for performance and specification and that is backed up by the long-standing relationships we have with customers around the world. We have worked with Honda for over 10 years as just one example. Our background and team is comprised of road and race car engineers for the most part, and that makes it easier for us to understand what our customers want to achieve. We speak their language. Our solutions are versatile and scalable as well. We offer a range of driving simulator products to cover everything, and in most cases, our simulators are quite modular and future-proof, so customers feel comfortable bringing them into dynamic workspaces.
I imagine it is also something that offers a sustainability benefit?
That’s another valid advantage of using simulators that we don’t often talk about, but our customers do. There are some real benefits beyond traditional engineering. For example, upon announcing its purchase, Continental said it will support the company’s goal to be the most progressive tyre manufacturer in terms of environmental and socially responsible business practices. This would support its aim to reduce real-world testing by up to 100,000 kilometres per year by 2030 and use 10,000 fewer tyres for development.
And are there use cases that were difficult to do beforehand that the Delta series S3 makes possible?
One example I like to cite is the validation of urban driving systems. To date, there have been challenges in trusting validations and eliminating the human immersion inconsistencies for drivers when testing blind spot or pedestrian detection systems. The Delta series S3’s 360° yaw capability and new 360° panoramic vision system offer a robust solution for this because the real-world urban driving events necessary to develop these systems can now be replicated 1-to-1 in the simulator lab.
And what about electric vehicles? Is the simulator useful for specific use cases?
The overall aim of a DIL simulator is to capture the subtleties of the human experience in a controllable and repeatable lab environment – and that’s a useful tool for any vehicle development – but we are truly seeing how beneficial this can be for new powertrains. For example, pedal behaviours and regenerative braking effects related to lift-off have a significant role in delivering an achievable (mileage) range for EVs. Virtual testing allows engineers to begin exploring this far earlier on, offering opportunities to confirm fundamental hardware before it is too late.
Another good example is towing with an EV. If you look at how an EV powertrain behaves while a vehicle is towing, our simulator gives the driver a real sense of the longitudinal acceleration and driveline behaviour, even on gradients. This means engineers get representative inputs fed back through the accelerator, and realistic throttle control behaviours from the driver. If you connect our simulator to hardware in the loop benches and load the battery, you can monitor the motor and the inverter in real-time. You will get a highly representative result with more real-world insight than you would with a pure desktop simulation.