Ben Smye explores the current trends in self-healing materials research, and where they might take the automotive industry in the coming years
It sounds like something out of a science fiction film, but the idea of a self-healing car might not be as wild and futuristic as it seems. Though machines that can fix themselves remain a long way off, materials engineers have been developing technology that could soon make this fiction a reality.
How do self-healing materials work?
The most well-known means for creating a material that can heal itself is to embed small capsules of healing agent inside the material itself. When the material is damaged, the capsules break and release the repair substance. However, the capsule size is crucial in this design, since if they are too big, the material will be weakened. They can also only be used once, which is not ideal if a material is likely to suffer repeated damage.
However, engineers have created self-healing materials that work through vascular networks, similar to veins on a leaf. In these microvascular materials, when there is a crack, healing agent flows through the vascular network and heals the break. This has proven to be effective, but it is also a slower method of repairing a material.
One challenge when creating self-healing materials that can be used in the automotive sector is that it’s much harder to create metals with these properties. Many vehicular parts are made of metal, but because of the chemical construction of metals and the way their atoms bond together, it’s difficult to create a self-healing metal. As a result, design engineers often concentrate their research on polymers.
Cars that never get scratched or can repair their own damages might be driving on the roads in the next few decades
Research into self-healing polymers has yielded ground-breaking results. It’s now possible to have a smart polymer that can regain its previous characteristics even after being damaged. Even more exciting is that materials scientists have been able to develop smart polymers called intrinsic polymers that can repair themselves without external stimuli. These intrinsic polymers have specific reversible chemical bonds, which means that they can recover their original properties.
Practical applications
All these developments are promising, but the question remains as to how these early steps in self-healing materials can be more than just curiosities from a laboratory. Many researchers are therefore exploring practical applications of their developments. For example, researchers are looking at the potential for self-healing polymeric coatings in a space exploration and deep-sea context. In these situations, a coating would reduce maintenance costs dramatically, as these are difficult places for repair work to take place.
These coatings are being designed for extreme environments, but should there be success in these sectors, the products will likely be made available in other areas. Some of the coatings being designed are anti-corrosive, while others are scratch resistant. These features are obviously useful for travelling to outer space and under the sea, but they would also be beneficial to vehicles that operate in less extreme conditions.
Painting cars is one of the major reasons for costs increasing during automotive maintenance. If the developments in self-healing polymeric coatings can create paint that can withstand minor scratches and resist corrosion, this could impact how much automotive operators have to spend on repairs. Even something this simple has the potential to extend the use life of vehicles, which would be good news for users.
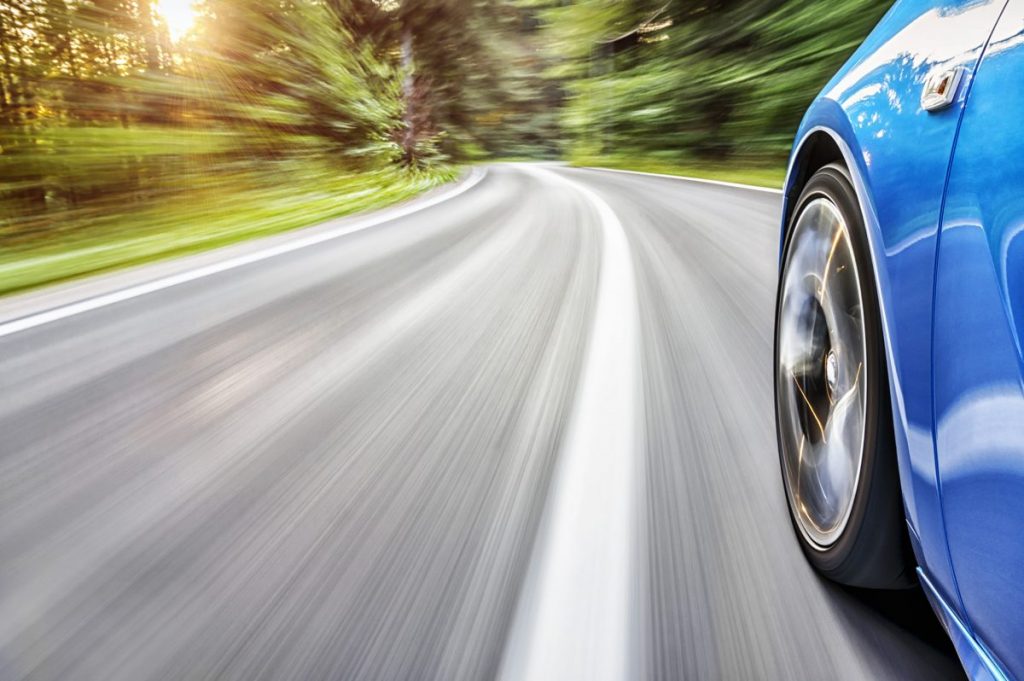
Reversible chemical bonds are also at the heart of another technological advancement. Researchers at Harvard University have developed a tough, self-healing rubber. To do so, they combined covalent and reversible bonds together by creating a molecular rope. The result is a transparent rubber that heals itself by distributing stress around the material.
When rubber cracks, it is usually because stress has become localised at one point. The molecular composition of the self-healing rubber prevents this from happening, as the material spreads the stress around through a network of crazes, which are essentially cracks that are connected by fibrous strands. By allowing the stress to be dispersed more evenly through the substance, the self-healing rubber is far more able to cope with force being applied to it.
Self-healing rubber has many potential practical applications. It could be used to make rubber bands that never snap, but the main use that the researchers have pointed out is tyres. Tyres made of this kind of rubber would be able to withstand more stress than the ones currently available, and would likely last longer, even in extreme environments. It’s even been suggested that should a tyre happen to be cut, if it was made of self-healing rubber, it wouldn’t need to be replaced immediately.
It sounds like something out of a science fiction film, but the idea of a self-healing car might not be as wild and futuristic as it seem
But perhaps we need to look beyond just cars themselves for the uses of self-healing materials. Road surfaces are easy to overlook when thinking about improvements in materials science. However, recent developments mean that as well as cars with self-healing properties, roads could also display these characteristics in the future.
In a promising development scientists have patented a self-healing concrete. Hendrik Marius Jonkers’s concrete includes bacteria that produce limestone, allowing the road surface to mend itself. Roads of the future thus have the potential to fill their own potholes. Pothole repair cost an estimated £1.3bn (US$1.84bn) in the UK in 2020, so developing a self-healing road could do more than just make for a smoother driving experience; it could reduce repair costs and potentially extend the driving lives of vehicles.
In the area of self-healing materials, it would seem that science is doing its best to catch up with fiction. However, it’s not there yet. Until then, design engineers should work on selecting materials that are best suited to the demands of their project. Design engineers need easy ways to research and compare various materials to choose whatever works best, and materials databases such as Matmatch can help.
For example, a polyamide material such as ForTii 11 provides optimal toughness for automotive electrical components. This high temperature polyamide contains halogen-free and halogen-containing flame retardants and performs well in harsh environments. It minimises the risks of cracking, and improves product reliability in terms of thermal shock ageing.
Futuristic cars that can mend themselves might not be available for purchase just yet, but research into self-healing materials is gaining ground every year. Cars that never get scratched or can repair their own damages might be driving on the roads in the next few decades. Though the technology is still being developed, materials scientists and engineers are turning the stuff of science fiction into science fact.
About the author: Ben Smye is head of growth at materials search engine Matmatch